ITMA 2019 : Game-Changing Swift-Jet Pre-Coating System Starts Worldwide Rollout
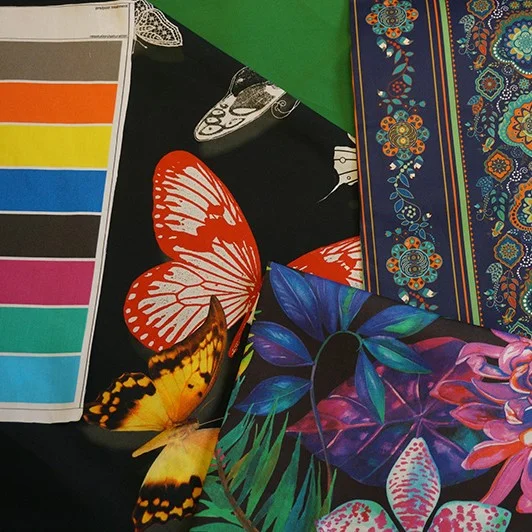
Image courtesy of Techni-Jet
The new Swift-Jet pre-coating system is a fully evolved technology of game-changing importance to any business engaged in digital textile printing.
Swift-Jet achieves the seemingly impossible by making on-demand small batch production perfectly commercially viable. As if that wasn’t enough, it greatly reduces operating costs, resource consumption and lead times for all users. It also makes it cost effective for smaller companies to have their own in-house end-to-end resource for textile printing.
Swift-Jet comes with quality guaranteed. It is the brainchild of Technijet Digital Ltd, part of UK-based Technijet. With a customer base covering over twenty countries, Technijet Digital’s focus for many years has been on reducing process costs and improving output quality.
Fully proven
Unlike many innovations that require something of a leap of faith from early users, Swift-Jet is fully proven and dependable. First announced at ITMA 2015, it has since undergone rigorous field testing and trials with leading textile printers.
As a result, the improved and enhanced Swift-Jet is an even more impressive performer, with plenty of real-world data available to help potential users quantify the achievable benefits. It will make its first major appearance at ITMA 2019.
‘This is an innovation with very significant benefits for both business and the environment,’ says Richard Hollweg, Technijet’s Business Development Manager. ‘We knew we had a winner from the start, but went through a deliberately exhaustive trial process to both prove and improve the product. We wanted to get Swift-Jet to the point where every potential user could be totally confident about buying into such a comprehensively new process.’
So what are the benefits of Swift-Jet?
• It makes short on-demand runs commercially viable and competitive, and delivers very large savings on longer runs.
• It is able to significantly reduce coating volumes which means lower chemical, energy and water consumption
• It reduces drying times.
• It reduces printing faults.
• It is extremely energy efficient.
• It can be used as a stand-alone for pre-coating reel-to-reel, or inline directly with a digital print machine.
• As an affordable in-house resource it improves creativity and productivity while reducing process time and dependence on third parties.
• It reduces waste significantly and makes environmental compliance much easier.
• it is easy to operate, so benefits and savings start immediately.
In short, it supports the future of digital textile printing.